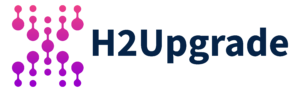
H2Upgrade transforms no-value, problematic waste streams (dilute industrial gases and solvents) into high value, concentrated H2 and CO2
The H2Upgrade Team
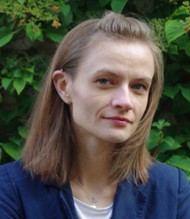
Dr Ewa Marek, University of Cambridge – expertise in water-splitting materials and reaction engineering.
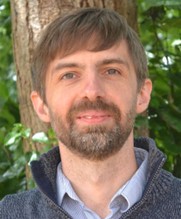
Prof. Stuart Scott, University of Cambridge – expert in high-temperature processes, process design, thermodynamic calculations
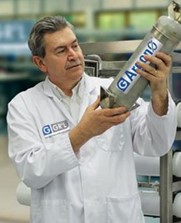
Dr Rob Grant (Gas Recovery and Recycle Ltd GR2l)– unrivaled technical and commercialisation expertise in using MOx materials to purify gases.
Introduction
The project consortium is led by the University of Cambridge and includes two Departments: Chemical Engineering and Biotechnology (CEB) and Engineering (CUED). The project is performed in collaboration with Gas Recovery and Recycle (GR2L) Ltd.
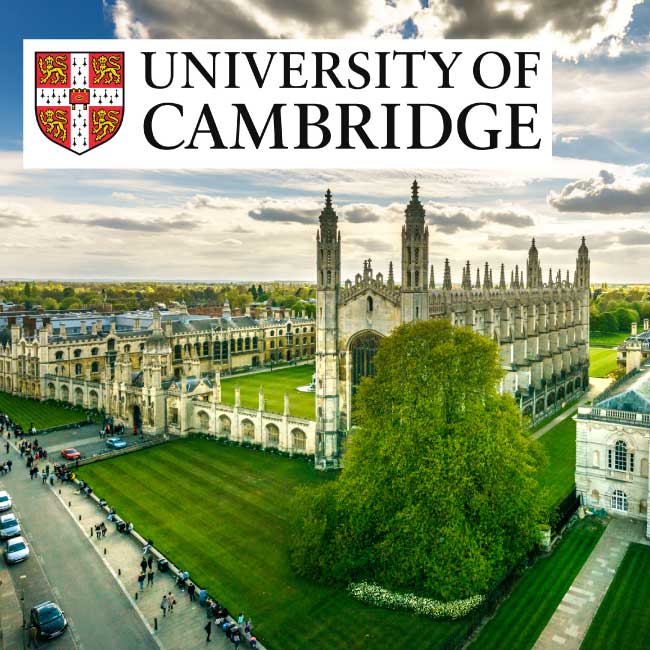
The Problems
Problem 1
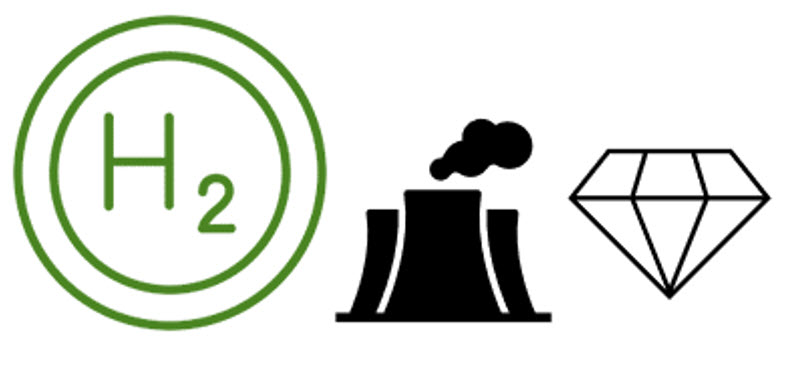
Technology is lacking to produce green H2 at middle/large scale
Incumbent methods for H2 production:
– Steam-methane reforming, which relies on natural gas, and so is not sustainable.
– Electrolysis of water, which does not scale well, is quick aging and relies on rare and precious metals.
Problem 2
Industrial waste streams
Commonly flared or released to the atmosphere, neither is environmentally benign.
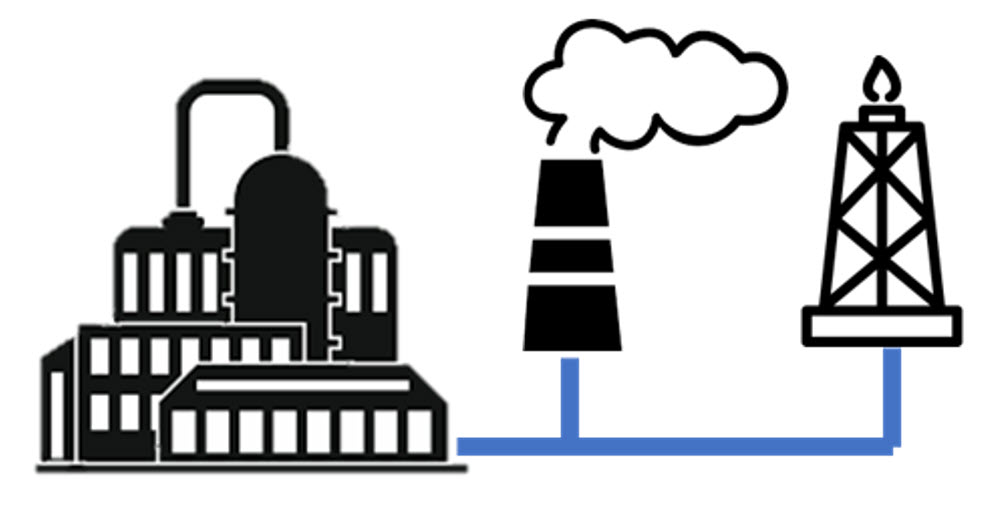
The Solution
Step 1
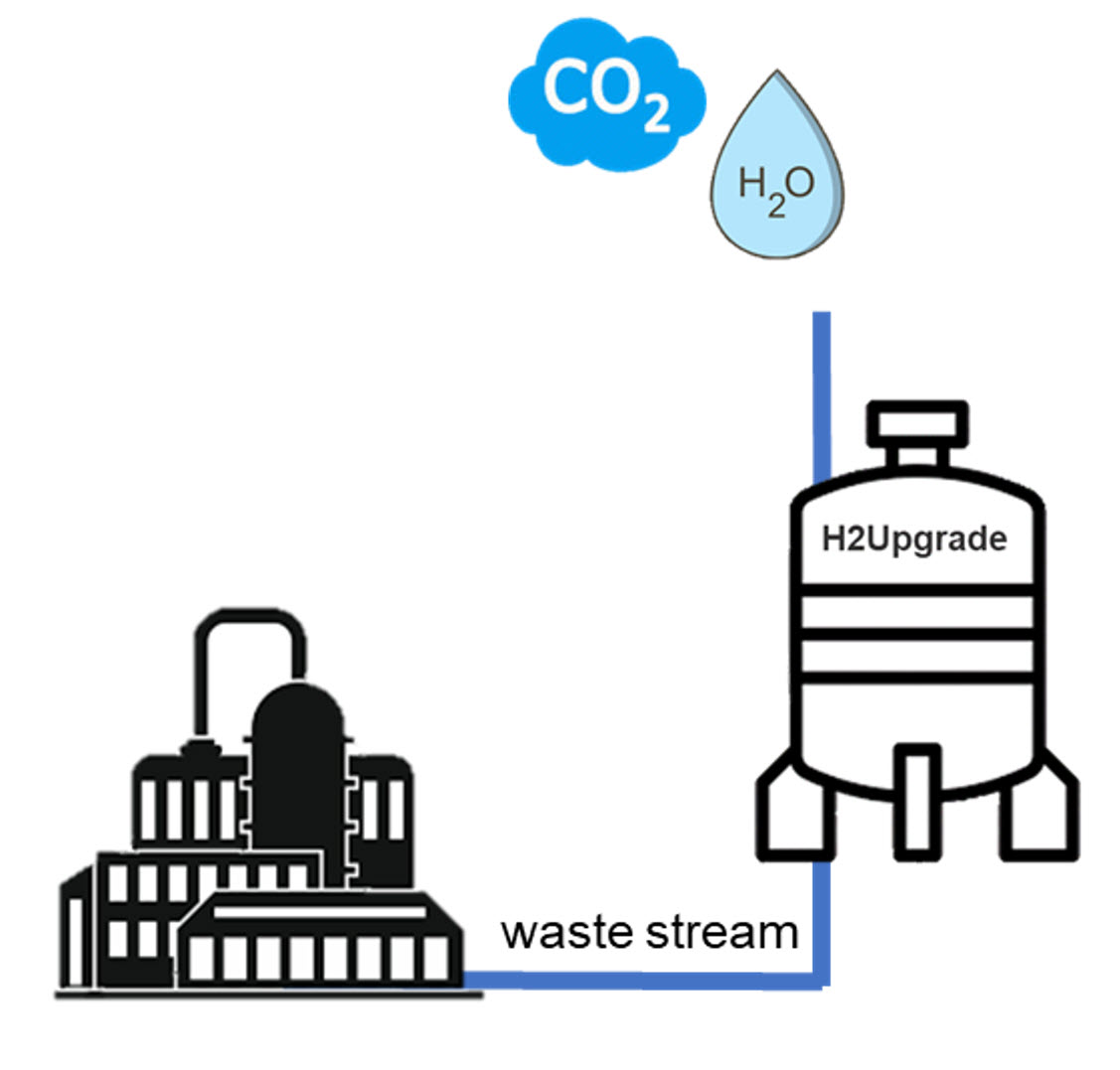
Pre activation of the H2Upgrade material* using industrial waste streams (dilute gases, solvents).
After liquifying H2O, the remaining CO2 is pure – ready for storage or for selling (e.g. for food production).
Step 2
Pre-activated material pulls out oxygen from H20 producing H2
High concentration H2 (up to 100%) – can be stored or used in house.
H2Upgrade materials are made of abundant and inexpensive metal oxides (Fe, Cu)
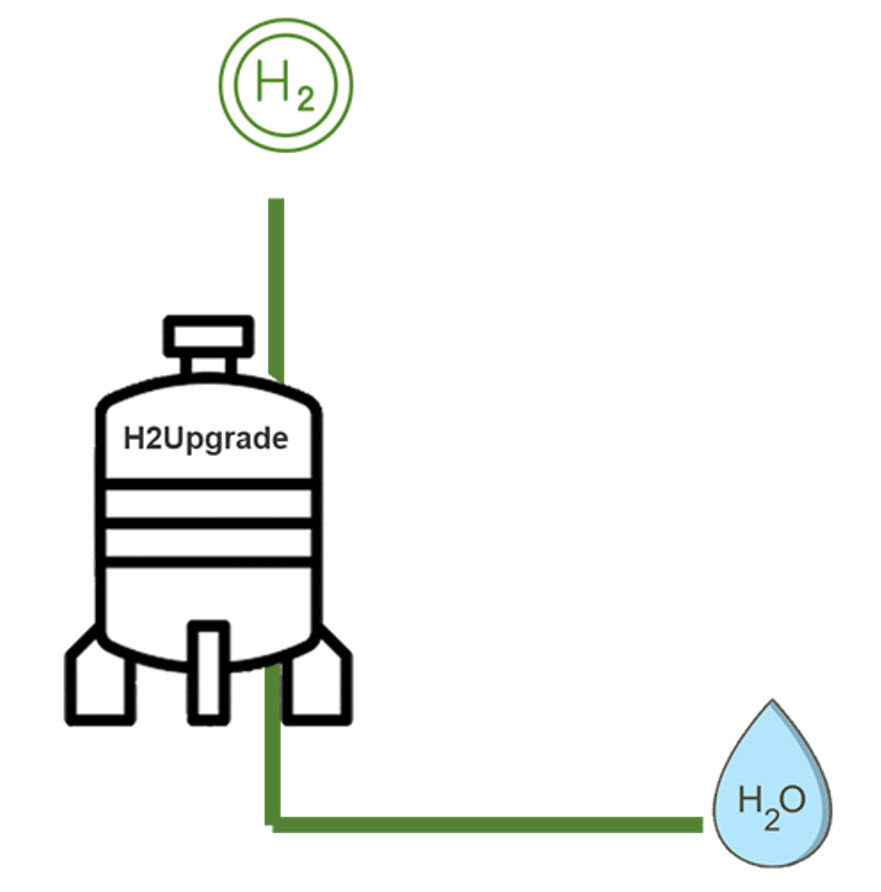
The Benefits
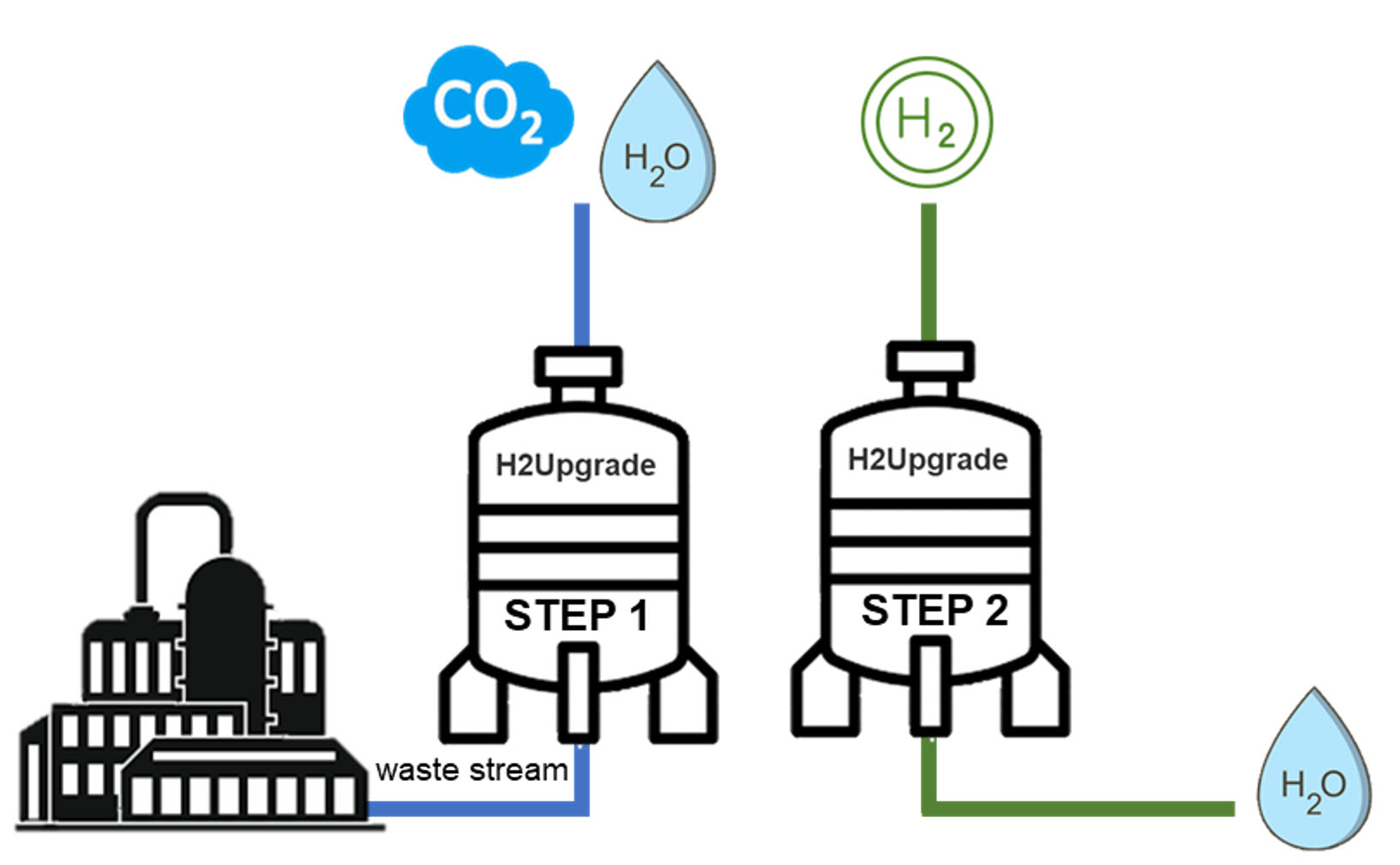
- Transforming no-cost, low-value waste streams into high-value H2
- Reduction of GHG emissions – produced CO2 is ready to capture, avoided CO2 from CH4 reforming
- Waste management – avoiding costs of purification and neutralisation of waste streams
- Acceleration of H2 economy with H2 production becoming attractive to waste-producers
- Simplicity – delivering an efficient on/off technology realised in medium scale units
- Mobility and flexibility of H2Upgrade units – mobile units to offer waste management service, compatible with various wastes
- H2 on demand – short start-up and shut-down
- Reliability, maturity, scalability –
- a well-known process, simple technology, can be designed and scaled as modular installations
Why Now?
H2Upgrade is based on a well-known steam-iron process, used for H2 production in the early XXth century
But steam-iron is not cost-competitive with steam-CH4-reforming
H2Upgrade – game changing features
- Using low-value waste streams for material pre-activation
- Using new materials capable of splitting water: high-performing perovskite oxides, based on inexpensive metals (Fe, Cu, Mn, Sr)
- Lowering process temperatures to enable efficient operations at small scale
- Flexible operations with different waste-stream – demonstrated in the lab
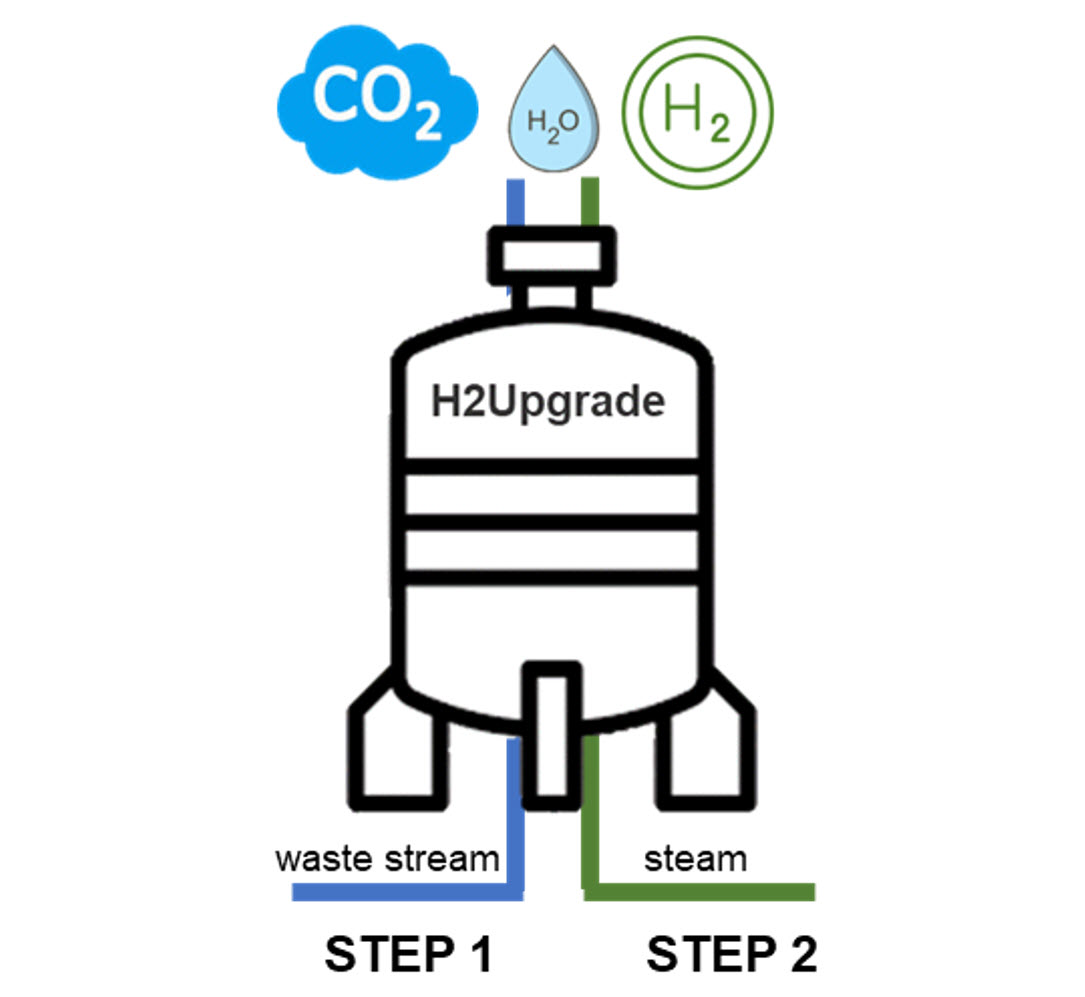
The Product
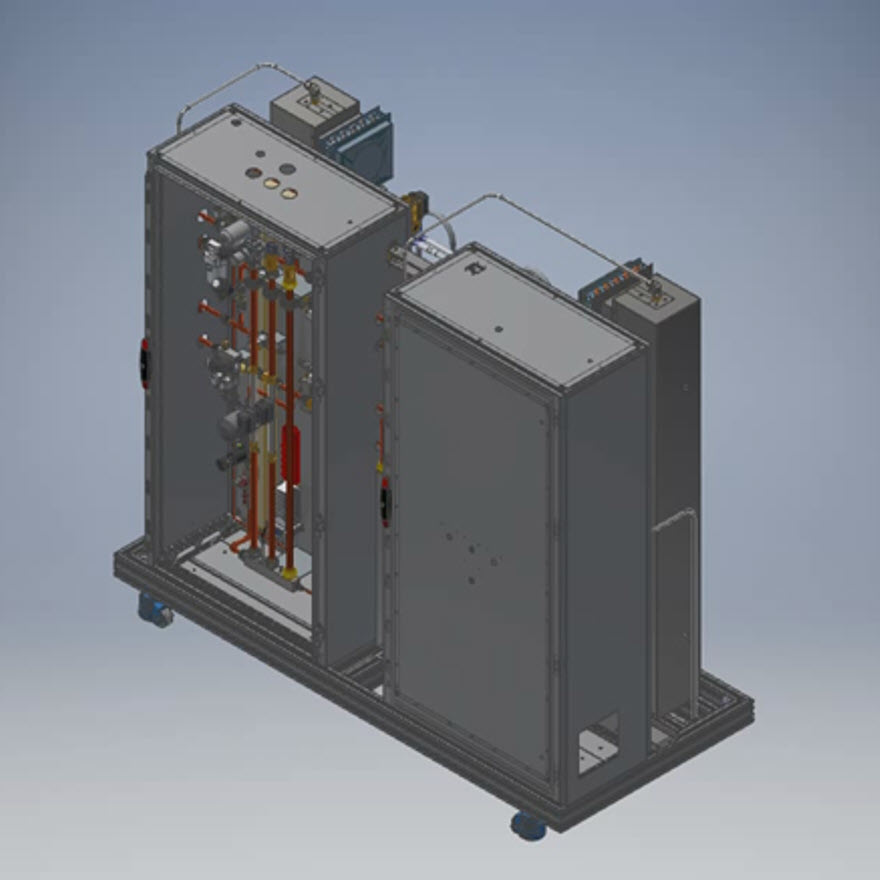
H2Upgrade units
Two-size modular units for 5-10 Nm3H2/h and 1-2 Nm3H2/h
Capable to work with multiple types of waste streams and waste-stream mixtures
Short start-up and shut-down times to support on-demand operations
Intellectual property – we have applied for two patents: one describing the process, another one describing our new catalytic materials